As a manufacturing engineer, I’ve seen first-hand how modern conveyor automation systems can transform manufacturing and packaging processes. I’d like to share some of the key benefits of industrial conveyor automation, focusing on product quality, efficiency, productivity, and analysis.
Product Quality
Let’s kick things off by talking about something every manufacturer cares deeply about: product quality. In today’s competitive market, ensuring that your products meet the highest standards is non-negotiable. Modern conveyor automation systems are game changers in this arena, offering advanced solutions that can detect defects, ensure proper placement, and maintain consistency.
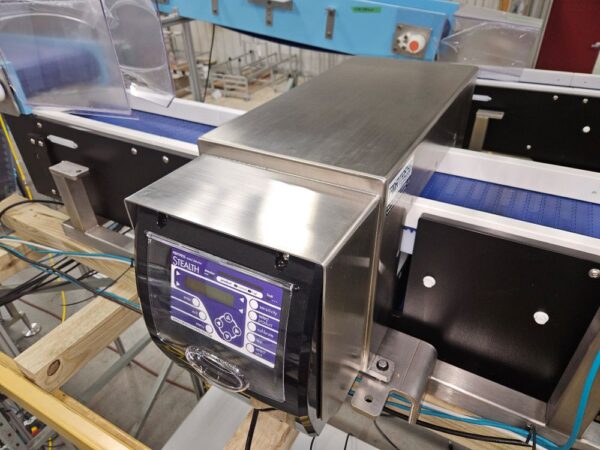
Metal Detection System
Let’s dive into how these technologies can elevate your product quality as well as your operational processes to new heights.
- Placement & Orientation: Proper placement and orientation are key for various downstream operations like inspection, packaging, and labeling and robotics integrations. Automated conveyor systems use advanced sensors to detect product orientation in real-time, minimizing errors and ensuring consistency. This not only improves product quality but also boosts production line efficiency.
- Metal Detection: Metal contamination is a big concern in many manufacturing processes. Automated conveyor systems with metal detection can quickly identify contaminated products, protecting consumers and machinery. These systems minimize containment process time and product loss.
- Leak Detection: In industries like food and pharmaceuticals, leak detection systems are a game-changer. They can spot even the tiniest leaks in real-time, ensuring only the best products hit the market. This cuts down on waste and boosts consumer safety.
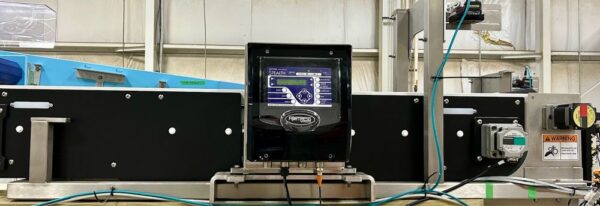
Metal Detection System
Now that we’ve explored how modern conveyor automation systems can elevate product quality, let’s shift gears and look at another crucial aspect: efficiency and productivity. After all, producing high-quality products is just one piece of the puzzle. Ensuring that your operations run smoothly and efficiently is equally important for staying competitive in today’s fast-paced market.
Enhanced Efficiency and Productivity
Imagine a production line that runs like a well-oiled machine, with minimal human intervention and maximum output. Sounds like a dream, right? Well, with modern automated conveyor systems, this dream can become a reality.
Let’s explore how these systems can streamline your operations and boost your productivity. Automated conveyor solutions can manage high volumes of products with minimal human intervention, leading to big efficiency gains and labor savings.
- Traffic Control: Techniques like accumulation, sortation, and singulation improve material flow, enhancing productivity, reducing downtime, and improving product quality. They create a flexible and responsive production environment.
-
- Accumulation: Temporarily holds products to prevent bottlenecks and keep operations smooth.
- Sortation: Directs products to specific destinations based on criteria like size, weight, color, shape, barcode, etc, improving order accuracy and throughput.
- Singulation: Separates grouped products into individual units for precise handling, enhancing accuracy and efficiency.
Vision Counting System
- Product Tracking: Bar code reading and RFID offer critical insights into product movement throughout the supply chain. This data ensures compliance, improves inventory management, and facilitates quick responses to recalls or quality issues.
- Machine Vision: Integrating machine vision with conveyors for product counting and automated inspection offers huge benefits. These systems ensure real-time quality control, reducing waste and rework. Plus, the data collected can improve production processes and support predictive maintenance.
- Box Filling: Automated box filling systems streamline packaging by accurately filling boxes with the right quantity of products. Boxes can be filled by weight or product count. These systems can manage various box sizes and product types, offering flexibility and reducing labor costs.
- Weighing and Dimensioning: These systems automatically measure product weight and dimensions, ensuring accurate data collection and improving packaging and storage. This reduces errors and rework, boosting overall efficiency.
Vision Counting System
- Automated Decision-Making: Modern systems can make decisions like sorting, routing, and quality checks based on programmed requirements, streamlining operations and reducing reliance on manual labor.
With efficiency and productivity enhancements covered, it’s time to delve into the world of data. Modern conveyor automation systems don’t just streamline operations; they also generate valuable insights. Let’s see how these systems can help you analyze trends and make informed decisions to continuously improve your processes.
Analysis and Trend Monitoring
In the age of Industry 4.0, data is king. Modern conveyor automation systems don’t just move products; they also generate a wealth of information that can help you make smarter decisions. Modern automated conveyor solutions generate valuable data that can enhance throughput and refine operations over time. From predictive maintenance to trend analysis, let’s see how these insights can drive continuous improvement.
- Data Outputs: Conveyor automation systems provide detailed reports on production aspects like speed, efficiency, and defect rates. This data helps find trends and areas for operational improvement.
- Predictive Maintenance: Using advanced sensors and data analytics, predictive maintenance systems will forecast equipment failures before they happen, allowing for pro-active maintenance scheduling. This minimizes downtime, reduces costs, and extends machinery lifespan.
- Process Enhancements: Continuous monitoring and data analysis help manufacturers make informed decisions to enhance throughput and efficiency, ensuring peak performance and profitability.
Turnkey System Solutions
Candidly, adding devices and components to conveyors is the easy part. Real magic happens with robust setup and programming. Controls engineers at Dynamic Conveyor are trained to understand your goals and can implement the hardware needed to make your industrial conveyor automation solution a success.
At Dynamic Conveyor, we specialize in turnkey solutions for modern automated conveyor solutions. Our system level approach ensures seamless integration of your production line, optimizing processes, reducing downtime, and ensuring top performance. Our commitment to quality and innovation means you can count on us for dependable, efficient, and adaptable automation systems tailored to your needs.
Summing it Up: The Benefits of Automated Conveyor Solutions
Modern automated conveyor solutions offer a host of benefits that can transform your manufacturing and packaging processes. From enhancing product quality to improving efficiency and productivity as well as providing valuable data for analysis, these technologies will drive innovation and excellence in the industry.
I’m excited about the future of automated conveyor solutions and its potential to revolutionize manufacturing and packaging. Whether you’re in food processing, parts manufacturing, or another general manufacturing or packaging industry, modernizing with automation will advance your business in ways you can’t imagine. Our team is ready to support you in your automation journey. Reach out to the conveyor design experts at Dynamic Conveyor to discuss your challenges and learn more about modern automated conveyor solutions for your plant.